Drying Equipment
According to different conduction modes, drying can be divided into conduction drying, convection drying, radiation drying, dielectric drying and combined drying.
The selection of ternary material precursor dryer needs to consider at least the following points:
- the moisture content requirements of the product;
- The moisture content of filter cake and whether the water content of filter cake is uniform;
- Production capacity of dryer and feeding mode of materials;
- The dryer in contact with the precursor of ternary materials need to be alkaline resistant, and metal impurities or other impurities can’t be brought in;
- Drying temperature to be reached, etc.
The precursors of ternary materials can be dried by hot air circulation drying oven, rotary dryer, disk dryer, rake dryer, microwave dryer & Vacuum belt dryer etc.
1.1 Hot air circulation drying oven
The shape of the hot air circulation oven is like a box, and the outer wall is an adiabatic insulation layer.
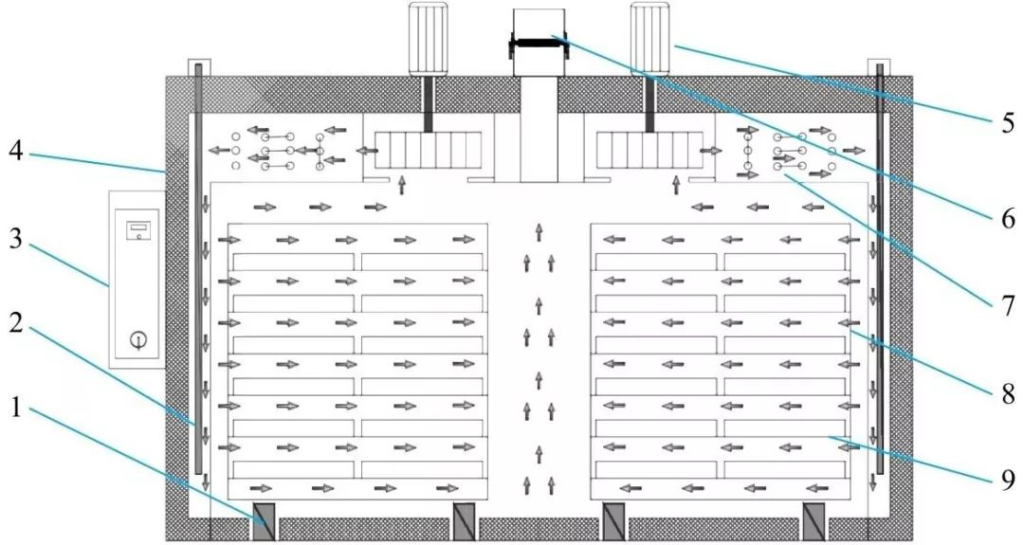
Internal structure drawing of hot air circulation oven
1 Caster 2 Thermocouple 3. Control panel 4. Thermal insulation shell 5. Fan
6 Exhaust port 7 heating wire 8 tray 9 tray support
The circulating hot air generated by the fan blows to the surface of the wet material to achieve the purpose of drying. The hot air circulates and dry the material repeatedly.
Advantages: easy loading and unloading, low loss, material tray easy to clean. Therefore, for the need for frequent replacement of products, high price of finished products or small batch materials, the advantages of the dryer is very significant.
Disadvantages: the material can not be uneven dried and dispersed, long time of drying, loading and unloading, more labors with low utilization of equipment; Dust flying when unloading materials, serious environmental pollution; Low heat efficiency is approx 40%, about 2.5kg of heating steam is consumed for every 1kg water drying.
1.2 Rotary dryer
The main body of a rotary dryer is revolving round drum with a small slope.
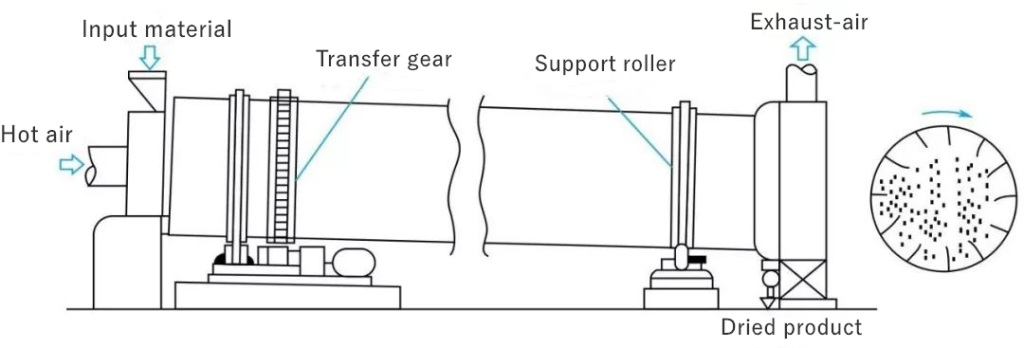
Advantages: large production capacity, continuous operation; Wide range of application, can be used for drying granular materials, for those with large adhesion materials is also very favorable; Easy to clean.
Disadvantages: high cost with difficulties on installation and disassembly; Low heat efficiency; The heating time to material particles is in great difference, so it is not suitable for the material with strict requirements on temperature.
1.3 Continuous disk dryer
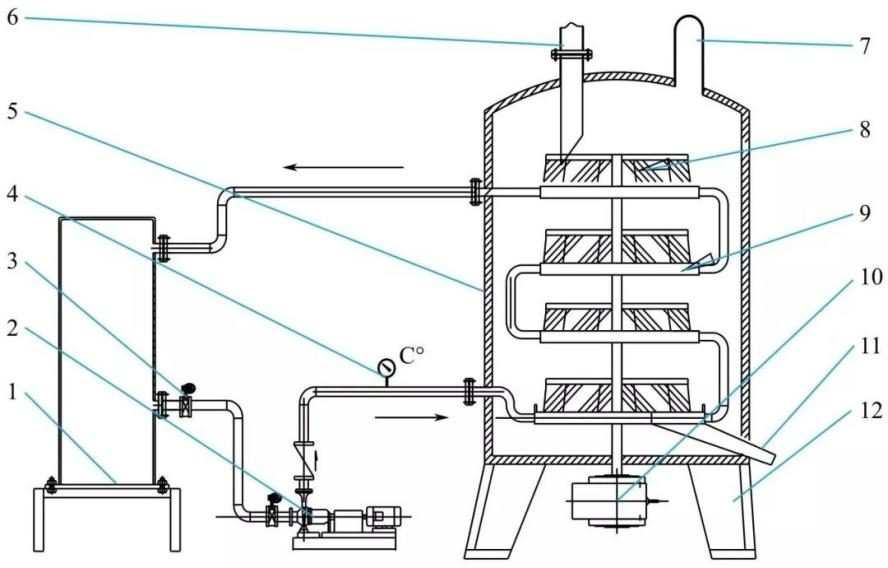
Structure drawing of disk dryer
1 Heat conduction oil tank 2 Hot oil pump 3 Stop valve 4 Thermometer 5 Continuous dryer 6 Feed port 7 Exhaust port 8 scraper 9 Heating plate 10 Reducer 11 Discharge port 12 legs
The hollow heating plate is the main part of the dryer, and the baffle plate or short tube is welded in a certain arrangement. On the one hand, the disturbance of the heating medium in the hollow plate is increased, and the heat transfer effect is improved. On the other hand, the stiffness of the hollow disk is increased and its bearing capacity is improved. Each heating plate is provided with a heat carrier inlet and outlet nozzle. Keep a certain distance between each layer heating disc, and fix it horizontally on the frame.
Advantages: high heat efficiency, low energy consumption & short drying time; Adjustable with clean environment;
Disadvantages: high nickel precursor powder is easy to damage when dry; difficult to replace line; The friction between harrow hand and disk surface is easy to lead to the increase of magnetic foreign bodies, and the cost of regular replacement of harrow hand is higher.
Note: The moisture content of the ternary material precursor filtered by the frame filter is higher. It belongs to paste material and can not adapt with disk dryer. Therefore, if the dryer chooses disk drying, the filtration and washing equipment in the front section needs to choose centrifuge.
1.4 Vacuum belt dryer
Vacuum belt dryer is a continuous high-efficiency &low energy dryer. The number multi-layer drying belt can be set according to the capacity of materials. The temperature is from 40 to 180℃, and the running rate can be adjusted.
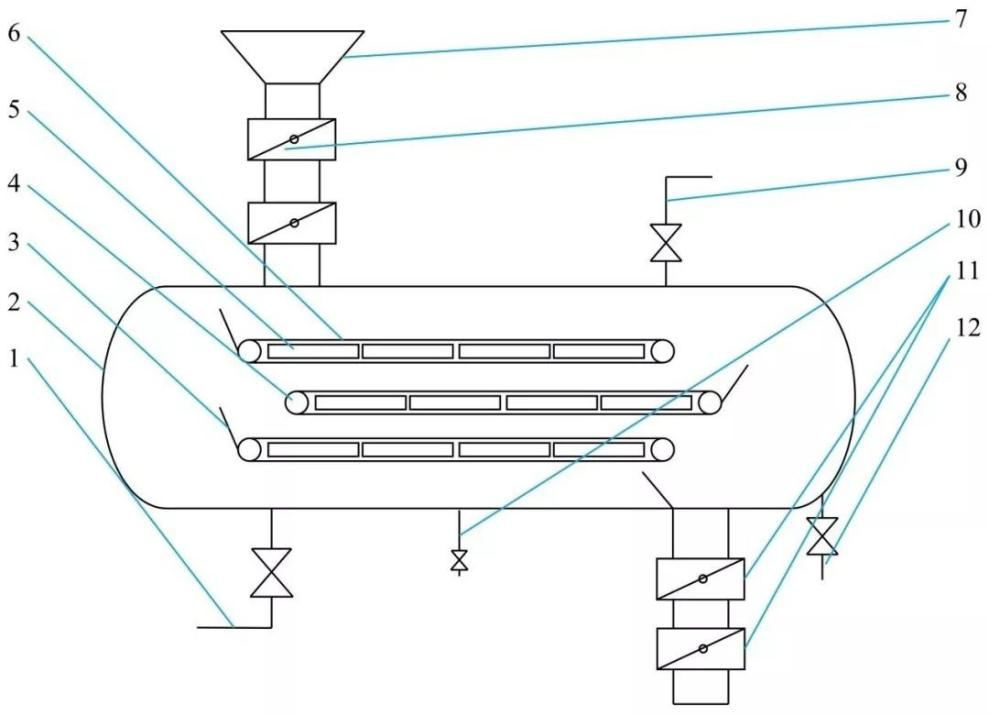
Structure drawing of vacuum belt dryer
1 Heat medium inlet 2 Shell 3 Block plate 4 drive shaft 5 heating plate
6 Belt 7 Feed port 8 Feed valve 9 Vacuum pipe 10 Drain port
11 Discharge valve 12 Heat medium outlet
Features: Complete continuous feeding and discharging under vacuum drying; High yield; The drying chamber of the product does not contact with metal, and the appearance is not damaged after drying. The drying process is easy to optimize and can be adjusted. Low energy consumption; Suitable for mass continuous automatic production.
Advantage of Vacuum belt dryer:
- Magnetic foreign body
The contact material is PP/PET material conveyor belt to avoid the contact between material and metal.
- Moisture content
Moisture content of discharge product is low and stable, fluidity is very good, loose without agglomeration
- Crystallographic Form
The material evaporates statically on the conveyor belt without destroying the crystal form
- Over-drying powder
Stable heating, no over- drying powder phenomenon
- Energy Consumption
Low energy consumption, energy saving and environmental protection
- Capacity
Continuous production and large processing capacity