Lithium hydroxide is an inorganic compound with the formula LiOH.(H2O)n. Both the anhydrous and hydrated forms are white hygroscopic solids. They are soluble in water and slightly soluble in ethanol.
In order to obtain battery grade lithium hydroxide from lithium brines, currently, in the conventional procedure, a brine with Li+ 4–6 wt% is fed to a process to form lithium carbonate and further used to produce lithium hydroxide. The disadvantages of traditional drying process are its high cost due to several stage requirement and the usage of lime, causing waste generation. The main objective of vacuum belt dryer is to demonstrate the feasibility of obtaining battery grade lithium hydroxide monohydrate.
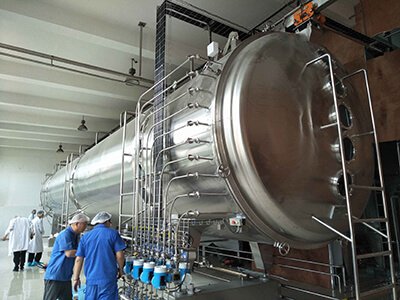
Instructing Installation
Tests showed that a current density of 1200 A/m2 and temperatures between 75–85 ◦C allow reduced specific electricity consumption (SEC) (7.25 kWh/kg LiOH). A high purity product is obtained at temperatures below 75 ◦C, with a Nafion 117 membrane and low electrolyte concentration. Resulting key electrochemical data would enable a pilot-scale process implementation to obtain lithium compounds.
The advantages of Vacuum Belt Dryer:
- Continuous feed and discharge under vacuum state
- Pipelined, continuous and automated drying process
- Adjustable Drying Temperature 20-200℃,low Temperature
Chemical drying process: Hydration and Dehydration Reaction
- 1/3 Running cost of traditional drying process
- Full enclosed and simplified process, no contamination
- CIP cleaning system, fulfill GMP requirement
- Drying time 20-150mins
- PLC control system
- Labor saving
- 98% Collection
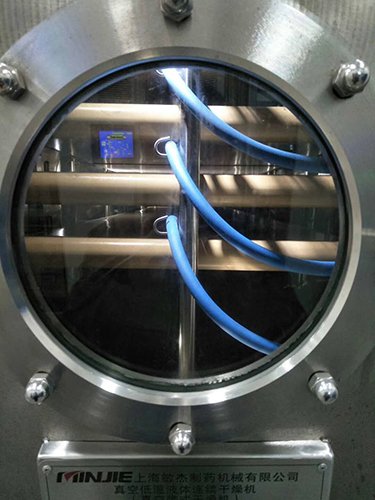
Vacuum belt dry for powder& particle
Can solve existing issues of traditional dryers:
· Metal magnetic foreign substance exceeds the limit
· CO3 2- (Carbonate ion) exceeds the standard level
· Air outlet causing powder running away, the on-site operation lead to unfriendly environment
· Easy to agglomerate, uneven moisture content directly impact
The hydration and dehydration of LiOH at various conditions have been experimentally investigated. The results show that the steam diffusion can be greatly enhanced at vacuum condition. A thin layer of LiOH is uniformly dispersed in the reactor, which can greatly increase the heat transfer between the LiOH material and reactor, leading to a higher hydration reaction rate of LiOH. Furthermore, the steam pressure, reaction temperature, and the particle size of LiOH can greatly influence the hydration reaction. A maximum hydration reaction rate of 80% is obtained under the conditions of 47 ◦C, steam pressure of 9 kPa, and particle size of 32–40 µm. LiOH exhibits a different reaction property at the condition of pure steam without air and below atmospheric pressure. A drying and reaction condition of LiOH with isolation of air is recommended when apply LiOH as a heat storage material at low temperature.